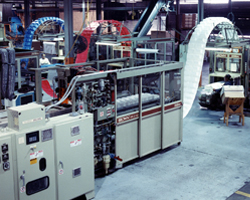


Custom Thermoformed Plastics
MarCon provides a broad range of thermoforming capabilities. Our John Brown equipment includes coil-fed, in-line presses with integrated trimming, three-station rotary formers and single-station formers. This variety of equipment allows us to compete on almost any thermoforming application, from small runs of industrial components to multi-million part packaging runs.
Most thermoformed components require some secondary trim or finishing operation. We have in-house wood and metal shops in which we design and build the jigs and fixtures to accomplish these tasks. Patterns and molds used in thermoforming are also constructed in-house.
Depending on part design, thermoforming can often provide significant cost advantages over other processes. Tooling investment may also be less costly than for other processes. We have supplied thermoformed parts to a diverse customer base for more than a quarter century. In this time we have honed our expertise in a manufacturing discipline which many consider an art.
Specific capabilities for the Plastics Division include:
- Vacuum and pressure forming, rotary press, 48 x 72 frame
- In-line coil-fed, 30 x 30 frame
- In-line coil-fed, 14 x 20 frame
- Various single-stage presses
- Custom product design
- Material selection
- Mold maintenance
- Automated mechanical assembly
Polypropylene (PP)
Polypropylene injection molding is a manufacturing method that uses polypropylene (PP) as the primary material to create plastic parts and products. PP is highly regarded for its outstanding characteristics, including strong chemical resistance, lightweight properties, and cost-effectiveness, making it a popular choice across various industries. The process involves melting PP resin, injecting it into a mold cavity, cooling, and potentially undergoing additional finishing steps. Celebrated for its versatility and cost-efficiency, polypropylene injection molding is a preferred approach for efficiently producing plastic components in a wide range of shapes and sizes. This method is especially favored in sectors like packaging, automotive, consumer goods, and medical devices.
Polystyrene (PS)
Polystyrene (PS) injection molding is a manufacturing technique that utilizes polystyrene, a thermoplastic polymer recognized for its transparency and rigidity, as the primary material for producing plastic parts and products. This method involves melting PS resin, injecting it into a mold cavity, cooling, ejecting, and potential finishing procedures. Polystyrene injection molding is frequently employed in industries that demand see-through characteristics and electrical insulating properties, making it a favored choice in sectors like packaging, electronics, and consumer goods. It presents a cost-effective and efficient means of manufacturing plastic components in various shapes and sizes, adeptly fulfilling the needs of these applications.
Recycled Polyethylene Terephthalate (RPET)
RPET, or Recycled Polyethylene Terephthalate, is a type of plastic material obtained from recycling used PET plastic items like bottles and containers. The recycling process involves collecting, sorting, cleaning, shredding, and reprocessing the plastic to create new granules or pellets. These recycled materials are then used to manufacture sustainable products, such as bottles, packaging, and textiles, reducing the need for new virgin plastic production and contributing to resource conservation and energy efficiency. RPET plays a vital role in promoting a circular economy and reducing the environmental impact of plastic manufacturing.
Polyvinyl Chloride (PVC)
PVC, or Polyvinyl Chloride, is a versatile and durable thermoplastic polymer known for its chemical resistance and wide range of applications. It is commonly used in construction for pipes, siding, and roofing, as well as in the healthcare industry for medical tubing and bags. PVC is an effective electrical insulator and is used extensively for wiring and cable insulation. It also finds applications in packaging, signage, vinyl flooring, and more.
Other Custom Thermoformed Plastics
Custom Colors Available!
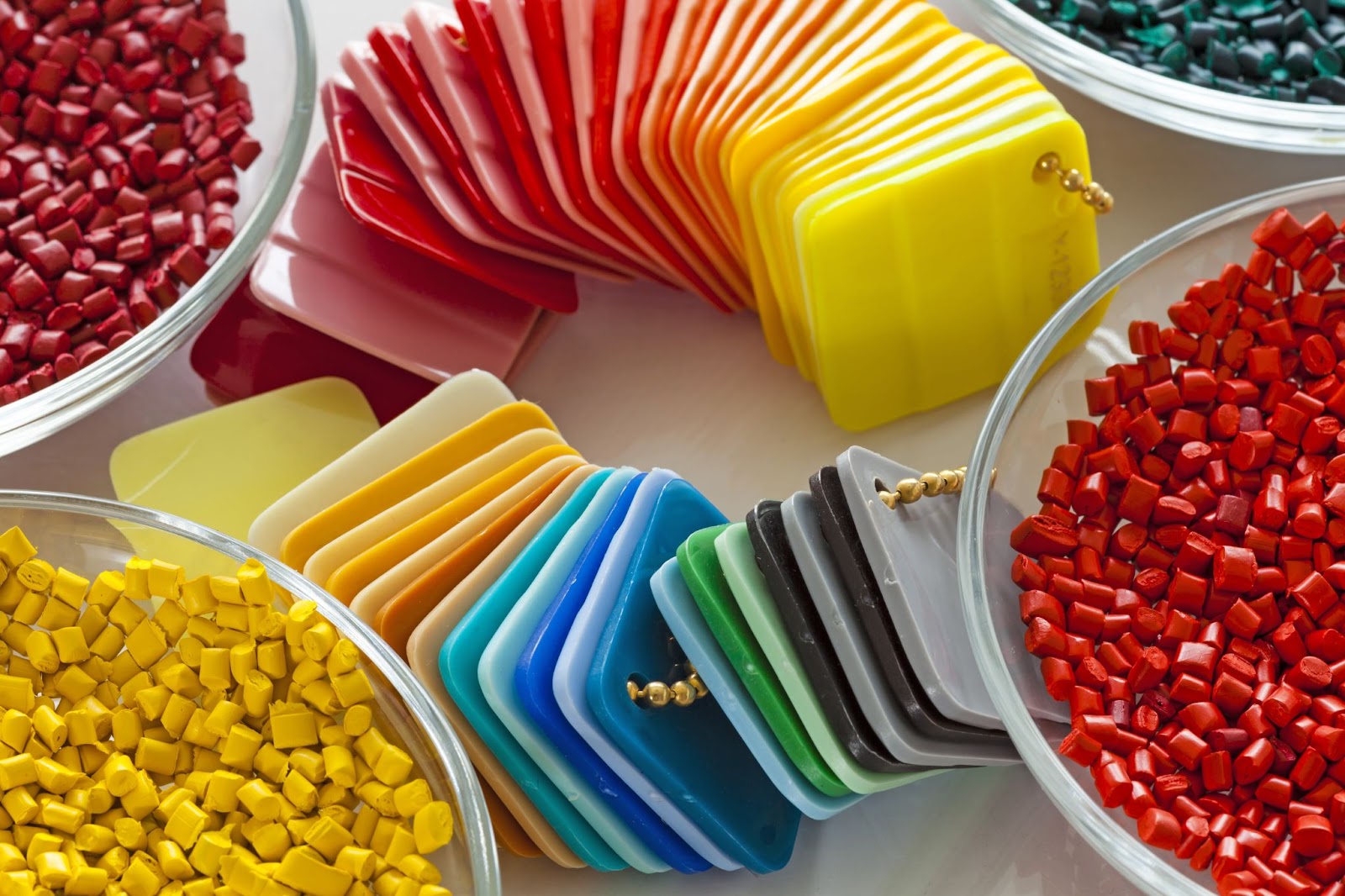
Colors in plastic injection molding are achieved by adding pigments or colorants to the plastic resin before it's melted and injected into the mold. Several methods are used, including masterbatch, pre-blended color pellets, dry color blending, and liquid colorants, each with specific applications. These colorants are mixed with the polymer material in the molding machine's barrel to achieve uniform color distribution. The method chosen depends on factors like the desired color, production scale, and precision requirements to ensure consistent and durable coloration in the final plastic product. Contact us today to learn how we can create the perfect color match for your project!
Quick Navigation
About Equipment Our Services Portfolios Products Plastics and Pop Display Solutions News Contact©2023 MarCon, Inc.® | ALL RIGHTS RESERVED | Industrial Website Catalog by WYSIWYG Marketing